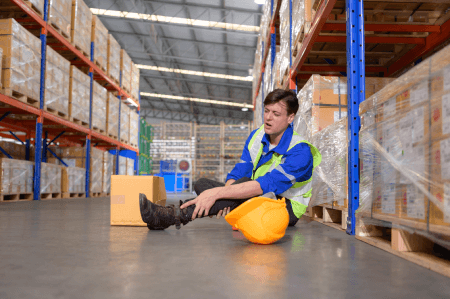
Maintaining slip safety in warehouses is no easy feat, especially when faced with high traffic, heavy machinery, and unpredictable environmental conditions. Slip and fall incidents can lead to costly injuries, operational downtime, and even legal liabilities. Enter tribometers, the unsung heroes of slip resistance testing. These tools provide an efficient and scientific way to monitor floor safety, ensuring that warehouses remain secure for workers and visitors alike.
In this article, we’ll explore how tribometers excel under challenging conditions and why they are indispensable for warehouse safety protocols.
The Role of Tribometers in Slip Resistance Testing
Tribometers are state-of-the-art devices used to measure the coefficient of friction (COF) on floor surfaces. This measurement helps determine if a surface is safe for walking under normal and challenging conditions. Unlike traditional methods of assessing slip resistance, tribometers provide accurate, real-time data, making them essential for proactive safety management.
In the fast-paced and often chaotic environment of warehouses, tribometers act as a safety net. Facilities managers can identify problem areas, evaluate cleaning methods, and select flooring materials that meet safety standards. By incorporating tribometers into routine maintenance, warehouses can significantly reduce the risk of accidents.
Why Warehouses Face Unique Slip Challenges
Warehouses are dynamic spaces where safety risks can emerge unexpectedly. Their unique challenges demand a tailored approach to slip resistance. Here’s why tribometers are a game-changer in such environments:
- High Traffic and Heavy Loads
Warehouse floors endure constant wear and tear from forklifts, pallet jacks, and heavy foot traffic. Tribometers help evaluate the durability of coatings and materials, ensuring they maintain slip resistance over time. - Spill and Contaminant Risks
Spills from liquids, oils, or grease are common in warehouses. Tribometers enable facilities teams to quickly test affected areas and determine whether cleanup efforts have restored safety levels. - Diverse Flooring Types
Warehouses often have mixed flooring-smooth concrete, textured coatings, or mats-depending on their layout and function. Tribometers are versatile enough to measure slip resistance across different surfaces accurately. - Seasonal and Environmental Variations
Temperature changes, humidity, and moisture can alter the performance of some flooring materials. Tribometers allow continuous monitoring to adapt safety measures based on evolving conditions.
How Tribometers Handle Tough Environments
Modern tribometers are designed with rugged applications in mind, making them well-suited for warehouses. Here are some of their key features that shine in challenging conditions:
- Portability
Many tribometers are compact and easy to transport, allowing users to test multiple areas quickly across large facilities. - Versatility
Whether the surface is wet, oily, or dry, tribometers provide reliable readings that reflect real-world conditions. - Digital Precision
Advanced models feature high-tech sensors and digital displays, ensuring accuracy even in fast-paced environments. - Durable Construction
Built to last, tribometers can withstand rough handling and harsh environments, making them a reliable choice for industrial settings.
Building a Tribometer-Based Safety Program
A tribometer is only as effective as the safety program supporting it. To maximize its impact, warehouses should incorporate these devices into a broader strategy:
- Schedule Regular Testing
Conduct routine slip resistance testing to ensure that high-risk areas meet safety standards consistently. - Train Employees
Empower your team with proper training on how to use tribometers and interpret their results. This ensures accurate and actionable insights. - Analyze Data Effectively
Use tribometer readings to identify trends, problem areas, and the effectiveness of current maintenance protocols. - Improve Continuously
Safety is an ongoing process. Use tribometer data to refine cleaning schedules, invest in better materials, or implement new safety measures.
Real Benefits of Tribometers in Warehouses
Adopting tribometers as part of a warehouse safety strategy offers tangible benefits:
- Fewer Accidents
Regular testing helps reduce slip-and-fall incidents, protecting workers and minimizing legal risks. - Compliance with Safety Standards
Tribometers ensure your facility meets industry standards, such as ANSI A326.3, demonstrating a commitment to safety. - Cost Savings
Preventing accidents reduces medical claims, downtime, and operational disruptions, offering significant financial benefits. - Employee Confidence
Workers feel safer and more valued when they know their environment prioritizes safety.
Tribometers as a Safety Asset
Warehouses are among the most challenging environments to manage for slip safety, but tribometers make it possible to meet and exceed safety standards. Their accuracy, versatility, and adaptability empower facilities to create safer workplaces, reduce risks, and maintain smooth operations.
Want to learn more about implementing tribometers in your safety program? Contact us today to discover how our tools and expertise can transform your warehouse’s safety protocols.